ESSICCATORI ZANDER
ADSORPTION TECHNOLOGY
DPS - DPS A
Cold regenerated adsorption dryers
- 7 to 85m³/h (at 1 bar with ref. to DIN /ISO 7183) at max. 16 bar over-pressure (KM 115 max. 15 bar over-pressure)
- Pressure dew point ratings -25°C, -40°C, -70°C
- Residual oil content up to 0.01 mg/m� at 20�C
- No TUV approval required
- for worldwide use with Variotronic controller
- Up to KM 35 wall mounted, KM 75 up to KM115 stand mounted
- ecodry KMA with additional activated carbon adsorber rating, residual oil content 0.003 mg/m³
ADSORPTION TECHNOLOGY
DPS 10-100
Complete preparation unit with pre- and post-filters incl. differential pressure display and autom. condensate drains (KEN 200 to KEN 1400)
- Output 130 to 5600Nm³/h (at 1 bar with ref. to DIN /ISO 7183) at max. 16 bar over-pressure
- Pressure dew points -25, -40, other PDPs on requests
- Residual oil content
- Pressure containers manufactured in accordance with CE type test (KEN 8000 and KEN 10000 with TUV)
- Stand mounted
- ecodry KEA with additional activated carbon adsorber rating, residual oil content 0.003 mg/m³ at 20°C
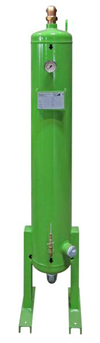
ACTIVATED CARBON ADSORBER SERIES
DSS
- Capacity levels 130 to 5600 m³/h (at 1 bar rel. to DIN /ISO 7183) at max. 16 bar over-pressure
- Maximum entry temperature 50°C
- Vessel made of quality steel acc. to CE, mounted on a frame
- With internal flow distributor, including pressure gauge and oil test indicator.
ADSORPTION TECHNOLOGY
DTS
High end adsorption dryer of the most recent generation, with externally heated dry part-flow regeneration.
- Output 420 m³/h to 14500 ³/min (at 1 bar with reference to DIN /ISO 7183) at max. 10 bar over-pressure, other ratings on request
- Pressure dew points -25, -40°C lower pressure dew points on request
- Patented vacuum process
- Maintenance-free 4 selector valve
- Corrosion-protected pipe bridges
- Energy-saving system
- No regeneration air
- Flange connections in accordance with DIN 2633
REFRIGERATION DRYING TECHNOLOGY
Freeze the humidity in the compressed air system!
Processing in the form of compressed-air drying or compressed-gas drying is necessary in most industrial and crafts processes. The aim is to avoid expensive interruptions of production. Therefore the required compressed air must be clean, dry and free from oil. Moisture in the compressed-air system (inevitable compressor condensate) usually causes end-consumer corrosion and damage, regardless of whether it is an impact wrench, a sensitive analytical system, or even breathing air is in question.
FST compressed-air refrigeration dryer systems have been designed specially for such heavy-duty applications. The output range with volume flows of 12m³/h to 6600m³/h in the well-proven standard range, and up to 100,000 m³/h in the case of large dryers, is implemented with the latest generation of refrigeration technology. Non-pollutant refrigerants that are not harmful to ozone, internationally available industrial-standard components and integrated solutions in the case of the components in a modular design, ensure permanent readiness ofr use and minimized running costs.